Spiral separator
The spiral separator is the best gravity concentrating equipment, especially for concentrating sand ore in seashore and riverside. It is made of the fiberglass, lined with wear-resistant polyurethane and covered with corundum cover. It has advantages such as lightweight, moisture proof, anti-rust and corrosion, noiseless, very suitable for the different feeding particle sizes and grades.
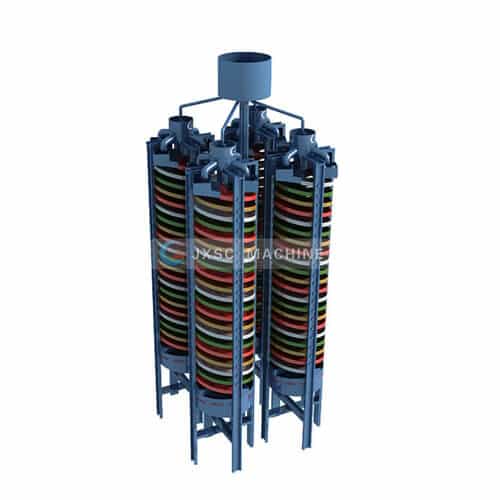
Capacity: 0.15-8t/h
Feeding size: 0.3-0.02mm
Advantages:
1. Simple structure, easy to operate and maintain
2. Low energy consumption
3. Relate wide range of particle size
4. Small volume, space saving
5. High productivity and efficiency
Main parts: ore distributor, feed chute, spiral chute section, cutting trough, collecting hopper, support, etc.
Spiral separator types: single spiral separator, lab spiral separator, rotary spiral separator, multi-deck spiral separator.
Application:
The spiral separators are designed for classifying the granularity 0.3-0.02 millimeters fine grain like iron, hematite, ilmenite, chromite, brasses, tin, tungsten, tantalum-niobium, gold ore, coal mine, monazite, rutile, zircon, and other Non-ferrous metal, rare metal, and non-metallic minerals with different specific gravity in the mineral processing plant.
Working principle of spiral separators
The ore materials are separated by the specific difference of gravity force, inertial centrifugal force, flow force, and surface friction of the light and heavy ore particles in the downward flow along the spiral tube slope.
Generally speaking, the movement of the slurry flow on the spiral concentrating tables surface produces two directions, one is the longitudinal flow which rotates swiftly around the vertical axis of the spiral chute and down along the chute surface, which is called the main flow, the other is the transverse flow which rotates around a balance layer of the ore flow itself, called transverse circulation flow or vice flow.
Under the comprehensive action of longitudinal main flow and transverse circulation, the mineral particles on the surface of spiral classifier move differently along longitudinal and transverse direction due to different density, particle size and shape, and settle at the bottom of the spiral groove in different time and speed, so the mineral particles are stratified according to density and particle size.
Stratification is the first stage of the separation process, which is basically completed after the first processing circuit of the spiral separators. After delamination, the light mineral particles in the upper layer flow to the outer edge of the spiral separator machine gradually, while the heavy mineral particles in the lower layer are affected less by the longitudinal main flow and move to the inner edge gradually. In this way, the layered particles are divided again, which is the second stage called zoning, completed after series ( 3-5 times ) sorting process. After the above two stages, the ore intercepting trough and the ore receiving hopper discharge the different grade separation products from the clay trough, and the separation process is completed.
The grain size distribution rule along the cross-section of the wet spiral separator is as follows: under normal ore-feeding conditions, more than 70% of the ore particles are concentrated in the middle of the spiral concentrator beneficiation area; About 20% of the ore grains are located at the inner edge of the chute; Less than 10% of fine ore grains are near the outer margin.
JXSC spiral separator manufacturer ( and other mining equipment) focuses on producing spiral gravity separator decades of year, qualified separator machines popular in the world market of various mineral processing. Contact us to the spiral separator price, installation instruction and special design service. Spiral separator for sale. Click to find more gravity concentration methods in mineral processing.
Tech Specification