Lithium is a high-value metal essential in producing batteries from smartphones to electric cars. As demand for lithium-ion batteries continues to grow, the need for efficient and cost-effective methods of extracting and refining lithium from ores has become increasingly important. Beneficiation is the process of removing unwanted minerals or impurities from ore to increase its value or quality. However, extracting and processing lithium from its ore is challenging due to its complex chemistry and the presence of impurities. Lithium ore beneficiation processes involve crushing, grinding, gravity separation, flotation and electrostatic separation to improve the grade and purity of the mineral product before it can be used for commercial applications.
Type of Lithium Ore
There are many types of lithium ores; the most common are spodumene, lithium petalite and lepidolite. Each ore type has unique properties that make it suitable for industrial applications.
- Spodumene is the most abundant lithium ore, usually containing 5% to 8% lithium (by weight). It is commonly found in pegmatite rock formations and can be extracted by conventional mining methods. Spodumene is widely used to produce lithium carbonate, which is used to make electric vehicle batteries.
- Lithium feldspar is another lithium ore typically containing 4% to 5% lithium by weight. It is found in granite rock formations and can be extracted through traditional mining techniques.
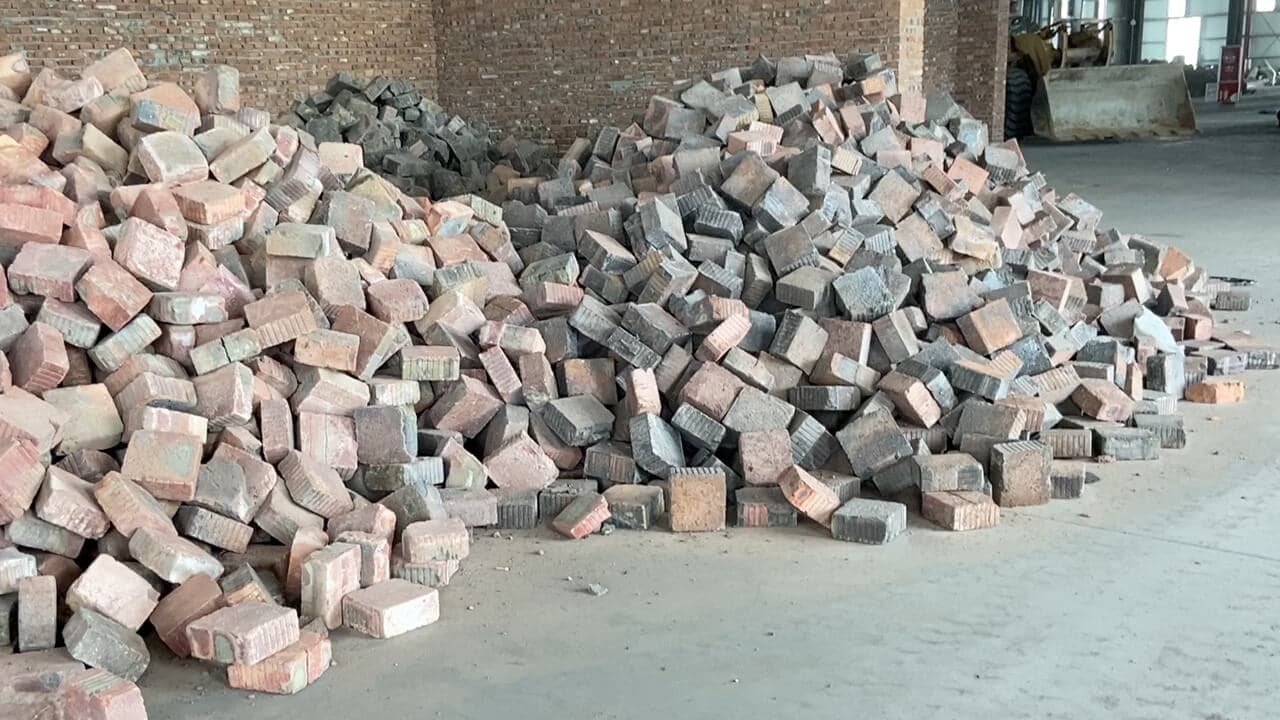
- Lepidolite is the most common lithium mineral and an important mineral for extracting lithium. Due to the low grade of lepidolite ore, the content of lithium oxide is usually 1.23% to 5.90%. It is a basic aluminosilicate of potassium and lithium, which is one of the mica minerals. Many impurities, accompanied by fluorine, aluminum, silicon, etc., result in complex refining and high cost. Lepidolite has unique physical properties, making it ideal for industrial applications such as lubricants, electrical component insulation, and heat-resistant materials.
Lithium Ore Beneficiation Process
Customized lithium ore beneficiation processes are critical to producing high-quality lithium products that meet the needs of the growing energy storage industry. By leveraging advanced technology and tailoring processes to the characteristics of each lithium mine, we can optimize operations and maximize production. Different lithium ore types require different beneficiation processes to extract the desired mineral.
1. Manual Selection
The hand-selection method is a method of preliminarily separating lithium ore minerals from gangue minerals by manual separation. It is suitable for concentrate enrichment and large crystal spodumene and beryl. According to the differences in color, appearance and luster between lithium ore and gangue, waste rock is manually sorted out to improve the grade of lithium ore in subsequent sorting operations. The labor efficiency is relatively low, the labor intensity is high, the selection index is low, and the waste of resources is serious.
2. Flotation Separation
Flotation is a lithium ore beneficiation method widely used in actual production, and the main minerals containing lithium can be sorted by flotation. Direct flotation and reverse flotation are two different flotation methods for lithium ore.
(1) Positive flotation of lithium ore
Positive flotation refers to the process of preferential flotation of lithium concentrate. The finely ground lithium ore slurry is added to sodium hydroxide for stirring and scrubbing to remove surface impurities. Then use oleic acid and its soaps as collectors to float the ore particles into the foam product in an acidic medium and obtain lithium concentrate. The concentrate is further processed to produce lithium carbonate used in batteries.
(2) Reverse flotation of lithium ore
Reverse flotation refers to finely ground lithium ore slurry. Dextrin and starch regulators are added to inhibit lithium concentrate in the alkaline medium adjusted by lime. The silicate gangue minerals are then floated out with a cationic collector, and the product left in the tank is spodumene concentrate.
3. Combined Process
Lithium ore often has complex associated components, and achieving the expected beneficiation index by a single flotation method is difficult. A combined process can be used for sorting, such as flotation-magnetic separation process, flotation-gravity separation-magnetic separation process, flotation-chemical treatment process, etc.
(1) Combined flotation-magnetic separation method
When the combined flotation and magnetic separation process is applied to the lithium concentrate obtained after the flotation method contains more iron to obtain low-iron spodumene, the subsequent magnetic separation method can be used to improve the quality of the lithium concentrate.
(2) Gravity-flotation-magnetic separation combined method
According to the density difference between spodumene and gangue ore, the coarser particle size lithium ore is sorted first. When the density difference between spodumene and gangue is greater than 0.2-0.5g/cm3, it is suitable to use a shaking table or jig concentrator for separation. When the density difference is less than 0.2~0.5g/cm3, the resuspension method can be used for separation. The lithium ore after gravity separation, can enter the flotation stage after desliming treatment. The lithium concentrate after flotation separation is further removed from iron impurities to improve the quality of the lithium concentrate and finally obtain a high-grade concentrate.
Understanding how to extract lithium is critical to producing high-quality products while minimizing environmental impact and costs associated with production. It involves crushing, grinding, flotation, magnetic separation and other methods to obtain high-grade lithium concentrate. It is recommended to conduct a lithium ore beneficiation test before sorting and putting into production, and at the same time, customize a scientific beneficiation process and equipment in combination with ore properties, investment budget and other comprehensive indicators to avoid resource waste. With the growing demand for lithium in various industries, including electric vehicles and renewable energy storage systems, JXSC adopts efficient and sustainable beneficiation processes to extract your precious resource.